Project Prometheus: Building Hundreds of Nuclear Power Plants to Make America Great Again
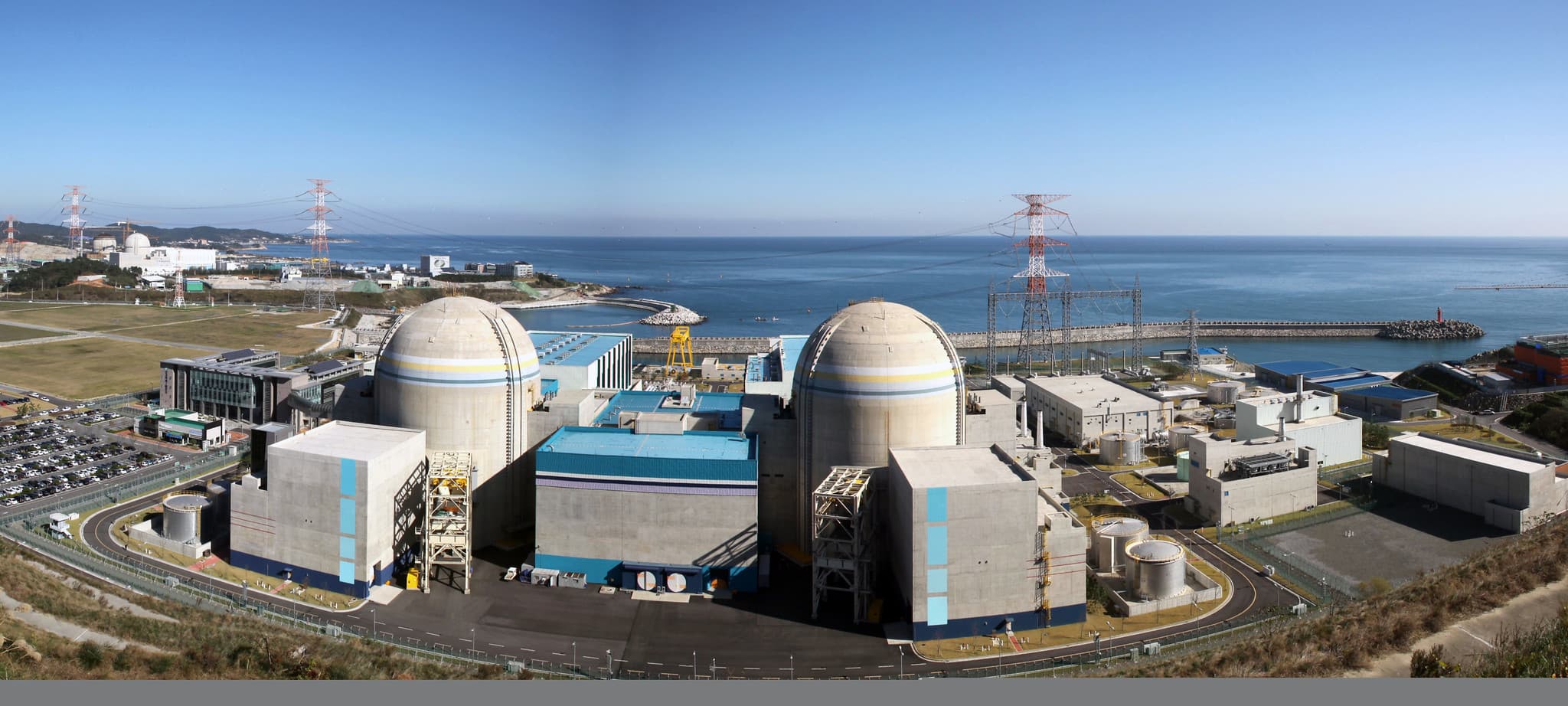
A note to readers: this is an old post on the archive website for Promethean PAC. It was written when we were known as LaRouche PAC, before changing our name to Promethean PAC in April 2024. You can find the latest daily news and updates on www.PrometheanAction.com. Additionally, Promethean PAC has a new website at www.PrometheanPAC.com.
We need on the order of 700 to 1,000 gigawatts of nuclear power to power our nation into the future. We can begin bringing new plants online over the course of the next five to ten years—transforming our entire economy by upshifting to a new scientific, industrial, and cultural platform. This will mean a transformation of our workforce—of upgraded pay scales, skill levels, and productivity. Much of this was discussed in this presentation.
We are going to need to produce hundreds of 1,000 megawatt (one gigawatt) nuclear power plants. To do this, producers of large reactors need the stability of large and consistent building programs and standardization of designs and the supply chains. This will also require the financing of a national bank, of public credit, as LaRouche PAC has specified. The private and remaining public utilities, as they exist today, will not be able to finance an investment of trillions of dollars or more over the coming decade or two. We must do this as a national mission.
As well, the new small modular reactors (SMRs), of 300 megawatts or less, also need to work out a range of designs and have the scale of demand which comes with a crash national nuclear power program, allowing costs to be reduced, so that they become efficient and effective in a range of applications, including desalination and process heat for heavy manufacturing and mining. The Trump presidency understood that these new SMR technologies, and the companies designing them, needed support to develop prototypes and to develop initial manufacturing capabilities to prove their undoubted potential. It also had to be shown that they have no technical flaws, and that their cost estimates are sound. That work is proceeding.
As will be outlined here, we are on the cusp of a nuclear energy breakout, with an insurgent new American Revolution afoot, led politically by President Donald Trump.
Do not be misled! The Uniparty inside the Beltway, the Biden collective, and the modern day British, “green/brown” Empire’s oligarchy that owns them, have another scheme. Their feudal drive would kill the construction of full-size ‘light water’ nuclear power plants altogether, and shackle SMRs to wind and solar. SMRs would merely serve as backstops, to add “resilience,” “when the wind don’t blow and the sun don’t shine.” Together with canceling fossil fuels, these feudal fascists would drive humankind down into Hell.
Instead, together with President Trump’s Artemis program to the Moon, Mars, and beyond, we must fire the imaginations of our younger generations, as one would fire up a forge! The colonization of space, together with Project Prometheus for nuclear power development, can be the context for training up our future productive workforce, utilizing a Space CCC program. See: Section 8, “Educating Our Youth—A Space CCC.”
Hundreds of American Nuclear Plants—Where and How?
Full-Size Light Water Nuclear Reactors
First, we must recognize what we have with the Westinghouse AP1000, the leading Generation III+ reactor in the world. With passive safety systems, a 60-year life span, up to 50% fewer safety-related valves, 35% fewer pumps, 80% less safety-related piping, 85% less control cable, and 45% less seismic building volume, the AP1000 design uses under a fifth of the concrete and rebar reinforcement of older designs. The AP1000 also has an 18-month fuel cycle for improved availability and reduced overall fuel cost. The world is learning about it, and so should you!
In April, China contracted for four more AP1000’s to be built in China. In May of 2022, Westinghouse Electric Company and South Korea’s Hyundai Engineering & Construction signed an agreement to “jointly participate in global AP1000 plant opportunities.” On Nov. 2, 2022, the Polish government announced that it had selected Westinghouse Electric Company’s AP1000 nuclear reactor technology to advance the country’s nuclear energy future. That could be for as many as six nuclear reactors. Besides the geopolitics of the Biden collective’s insane drive for war with Russia, what does this tell us?
Part of the Polish backstory is that in September, Westinghouse announced Memoranda of Understanding with 22 companies in Poland for cooperation on construction and labor force development to build AP1000 reactors in Poland and at other potential projects in Central Europe. “Westinghouse has committed to establishing a major engineering center and is planning various additional industrial investments to support training and development of Poland’s nuclear power talents and workforce. Westinghouse contemplates engaging on a broad scale both the U.S. and European supply chains on this exceptional project, in order to build a fleet of AP1000 reactors in the region.”
Well, the same can be done, and must be done, here in America! And these projects, engineering centers, and construction sites can be training grounds for our youth.
The Myth of Construction Costs
The old saw is that nuclear power plant projects take almost 20 years, 8-10 years to plan and some 8-10 more years to construct. Not true. Faster construction has been underway in South Korea, where standard designs were constructed sequentially on a limited number of sites and with a stable supply chain. The South Koreans have achieved nuclear plant builds of less than five years; we can too.
A South Korean example of mass production methods that work is Doosan Enerbility's integrated nuclear component manufacturing facility in Changwon, South Korea, now being tapped by NuScale (see below). Doosan is proud of being the largest global supplier of nuclear power plant components for the past 40 years.
South Korea has shown the way in building a series of 900 and 1,000 MW reactors of a standard design. Ironically, their chosen design was licensed from Combustion Engineering (C-E), now headquartered in Stamford, Connecticut. Indeed Combustion Engineering has been building steam boilers since 1904, moving up to nuclear steam supply power systems. Beginning in 1995, with that C-E design, South Korean companies built a dozen C-E-derived reactors using the same elements in the supply chain. C-E’s nuclear division is now part of Westinghouse. Beyond this, South Korea’s Generation III APR1400 draws on C-E System 80+ innovations. Throughout, they minimized (though not eliminated) design change, reduced construction time, and reduced capital costs by some 30%.
Additional studies, as well as South Korea’s results, have also shown that the real cost and complexity of nuclear construction is not in the heavy forging and high-tech vessel and turbine manufacturing costs, but the site construction work (concrete structures, mechanical equipment and electrical systems) and related design (& redesign) and supervision overheads.
“Green” anti-nuclear efforts, funded by Wall Street outfits like the Natural Resources Defense Council (NRDC) have added to the “red tape,” in addition to construction constraints already varying widely from site to far-flung site. It is assessed in the US and Europe that around 50% of total project costs are in the nuclear site construction & design costs. These costs become even higher as a project takes more and more time to finish.
However, with standard designs, constructed sequentially on a limited number of sites and with integrated stable chains, these costs are overcome. One improves site productivity by learning lessons from one project and applying them to the next project.
Standardization is, after all, the precursor for successful modularization. We, as Americans, know how to do this. In many ways, we invented this approach, going back to Samuel Colt and Eli Whitney and successful standardized production of Colt revolvers beginning in the 1850’s!
Such standardization allows for ‘production learning.’ That is, the mastery of, and improvements in, a production process which comes with the actual “scaling up” of physical production—thereby achieving “economies of scale” where costs fall progressively as manufacturing volume is increased. The inherent process of human discovery, including engineering and worker input, transforms the very production process itself.
As more than one specialist has asked, “Why does this not occur in nuclear?” The reasons are simple. Nuclear energy development has been systematically sabotaged. Nuclear projects are marred by frequent design change and therefore bureaucratization. In the process, supply chains are constantly in flux, with potential small- and medium-sized suppliers losing the benefits of experience.
Now we have a golden opportunity with the completion of the Vogtle nuclear plants #3 and #4 in Georgia, the first new nuclear plants in 30 years. The frequency of nuclear production has been far too low for knowledge to be captured and shared. Now, another generation of skilled construction workers, engineers, and managers, numbering some seven to eight thousand, have been trained-up building the most advanced AP1000’s. These skilled men and women can and must be rehired and “redeployed” to new, additional nuclear plant construction sites, training others. We can do it, through a multiplier effect!
We can, in short, build up the capacities, logistics, and manpower for advanced 1 gigawatt power plants—to go nuclear!
LaRouchePAC needs your financial support. Donate today and help grow our operations.
Small Modular Reactors (SMRs)
Lets move on to SMRs, the new element in the big picture. In addition to Nuscale, Terra Power, X-energy, Rolls-Royce SMR Ltd., and many other companies are developing factory-built SMRs that will offer clean, affordable energy.
The small reactors are to be built in factories, with little or no in-field fabrication or construction. We are moving from standardization of full-sized plants and bringing the benefits of modularization to bear. What if it only took 12 months to produce a reactor pressure vessel? Which methods can we bring forward to accomplish this in the near-term? The Electric Power Research Institute (EPRI), in a 2018-2019 advanced manufacturing program done with companies including NuScale, has identified a host of new technologies that move us in that direction:
- Powder Metallurgy-Hot Isostatic Pressing (PM-HIP)
- Electron Beam Welding & Heat Treatment—one pass welding
- Diode Laser Cladding
- ATLAS—Advanced Large Scale HIP
You probably are not familiar with these technologies, but you can easily look them up online. They are technologies that are part of the transformation of advanced manufacturing, and can be applied to SMR nuclear reactor construction. As well, modular construction is not new. This is recognized in both ship building and in chemical plant construction. It has also been demonstrated in the construction of nuclear submarines. Combining a smaller power plant footprint, fewer components per power module, and a high percentage of modular factory-fabricated components and packages, reduces construction complexity and duration. Quality assurance, inspection, and testing activities are also more easily performed in a factory, and can work to insure an on-time construction schedule and improve cost certainty. However, in adopting modularization, it requires the development and use of contractors and suppliers that can work to the closer tolerances and higher quality standards that are required for success. Developing our workforce remains essential!
The Example of NuScale
Let us turn to the example of NuScale Power modular factory production—not because it is the most scientifically and technologically advanced SMR builder, but because NuScale has been certified by the Nuclear Regulator Commission and its power module is in an advanced stage of development. Where are we in the process of bringing this modular factory production of nuclear reactors into being?
NuScale Power’s first commercial 6-module VOYGR power plant is now planned to be built on a site at the Department of Energy’s Idaho National Laboratory. It will be owned by the Utah Associated Municipal Power Systems (UAMPS) and the first module of the NuScale VOYGR-6 power plant (462 MWe) will begin generating energy in mid-2029; the remaining modules will come online for full plant operation by 2030. NuScale hopes to have other plants in operation, for example in Eastern Europe, by 2026 or 2027.
Each NuScale Power Module (NPM) is to be factory built—including containment and reactor vessel. It may be assumed that an initial factory for production of these NPMs will be built in that vicinity of the Idaho National Laboratory. The development of this embrionic factory manufacturing process has been accomplished with the aid of the first Trump presidency, the Department of Energy, EPRI, research institutes, and universities.
Looking at NuScale’s current progress, we have a window onto the larger SMR factory-manufacturing process itself:
- In 2018, NuScale selected Virginia-based BWX Technologies to start the engineering work to manufacture NuScale’s SMR.
- Standard Plant Design activities are now in progress with support from Sargent & Lundy and Fluor Corporation. NuScale has a longstanding partnership with Fluor as both investor and engineering, procurement, and construction (EPC) service provider for NuScale’s NPM technology.
- On April 22 of this year, NuScale signed a collaboration agreement with the US Reactor Forging Consortium (RFC) “to leverage the existing robust forging supply chain in the US, to prepare NuScale to deploy its SMR technology to customers worldwide, and to support, retain, and expand US manufacturing jobs.” The RFC comprises three companies—North American Forgemasters (NAF), Scot Forge, and ATI Forged Products—which together are the only fully integrated American manufacturers of as-forged piece weights exceeding 160 tons. These include large alloy and stainless steel open die, seamless rolled ring, and large uniquely shaped forgings. NAF has its principal office in New Castle, Pennsylvania; Scot Forge is headquartered in Spring Grove, Illinois, and ATI Forged Products has its office in Cudahy, Wisconsin.
NAF is also partnering with the Pennsylvania-based Center for Advanced Nuclear Manufacturing (operated by Concurrent Technologies Corporation), on a full production size shell research project that will focus on the use of austenitic stainless steel for reactor and containment vessels in SMRs and advanced reactors.
This is the kind of work that must be expanded, through the use of national public credits, and replicated nationwide.
- NuScale then signed on April 24th with South Korea’s Doosan Enerbility, formerly Doosan Heavy Industries & Construction, and again with BWX This work begins with design for actual manufacture, assembly and transportation, of the NuScale Power Module. Doosan has begun production of forging materials with full-scale equipment manufacturing expected to begin by the latter half of 2023. Manufacturing will presumably take place at Doosan Enerbility's integrated nuclear component manufacturing facility in Changwon, South Korea. That facility has a range of manufacturing capabilities, from raw material production to final assembly of nuclear components. Doosan has manufactured and supplied 34 reactor vessels and 124 steam generators globally. These include reactor vessels and other main components for Hyundai Engineering & Construction’s build of the large Barakah nuclear plant complex in the United Arab Emirates.
- In Canada, since 2019, NuScale Power has also been advancing the manufacturing process development work at BWXT Canada Ltd.’s facility in Cambridge, Ontario in preparation for the fabrication of the NuScale Power Module. BWXT Technologies, Inc is a leading global supplier of nuclear components and fuel. BWXT is the only North American company to continuously manufacture nuclear steam generators for the commercial nuclear power industry since the 1950s. “... NuScale estimates that 80 percent of the content for the NuScale power plant could be sourced by the existing Canadian supply chain capabilities. This includes opportunities stemming from BWXT Canada as it plans to engage sub-tier suppliers related to the reactor pressure vessels such as forging, precision manufacturing and material supply, steam generator tube bending and specialty services.”
In Conclusion
So the work is on and ongoing. We are not starting from a dead stop. Hopefully, enough has been presented here to fuel the imagination. It will surely take President Trump and the American people to bring our Project Prometheus for a nuclear renaissance to the point of bearing fruit. It is a commitment to allow the future to once again guide our nation’s course. It must fire the imaginations of our youth. It will require the mobilization of public credit made available through a National Bank. It will require the fulsome deliberations of the American people, befitting our Founding Fathers and our Constitutional republic. It will be a renewed national commitment to advancing science, technology, and humane culture, willed into being by all of our efforts.
LaRouchePAC needs your financial support. Donate today and help grow our operations.